The Process
Fiber composites are divided into thermoset and thermoplastic composites based on the matrix used. Due to low material prices and the largely mastered processing techniques, fiber-reinforced thermosets have been historically predominantly used. To achieve a high component quality, all thermoset production processes also require a subsequent manufacturing step to cross-link the thermoset matrix under pressure and temperature. The resulting additional cycle times tie up production resources such as molds and ovens, which reduces cost-effectiveness and sets capacity limits for production.
The use of thermoplastic matrices offers the potential for fully automated production in addition to the utilization of material-specific advantages, such as higher impact strength. Unlike thermosets, which harden within hours due to time-consuming chemical crosslinking, thermoplastics solidify within seconds because of physically induced phase transformation when cooling from the melt.
Among the available methods to produce fiber-reinforced thermoplastic components, tape placement and tape winding have the most potential for fully automated production. Tape placement is particularly suited for small to medium-sized series production of complex molding components with large surface areas, while tape winding is well suited to high volume series production. The use of a laser as heating source, in contrast to hot gas or open flame processes, allows tightly controlled temperature ranges with a quick and precise temperature control system thus allowing an integrated, online quality control during the production.
With the aid of laser-assisted, thermoplastic tape winding and placement (LATW/LATP), it is possible to produce high-strength, high-stiffness components with a low structural weight. The process runs as follows:
- A placement head positions the pre-impregnated tapes, on the required mold or mandrel
- The thermoplastic pre-impregnated tape material is heated by a laser to the processing temperature
- A fast control system maintains the desired parameters such as process temperature, consolidation pressure and tape tension.
- The LATW process results in a composite component which is ready to use (in-situ consolidation)
- All process parameters are logged to be used for quality assurance.
Market Applications
The simplest component forms that can be realized with LATW/LATP technology are tubular or flat structures. At AFPT, we specialize in the following types of parts which have wide applications in automotive, oil & gas, infrastructure, consumer products and aerospace markets.
Thin-Walled Inserts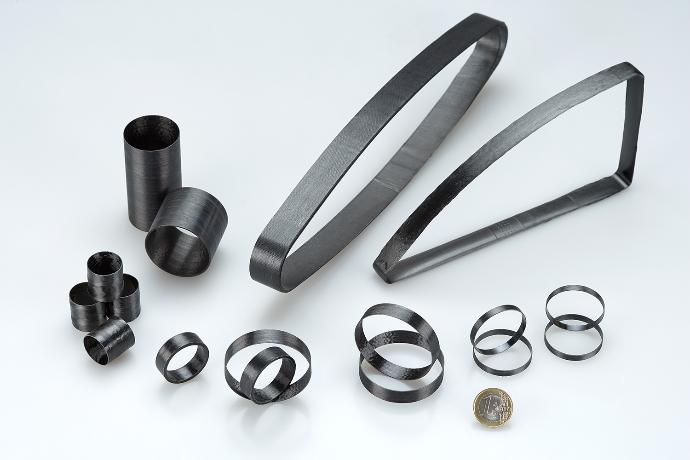
Thin-walled ring, sleeve, or bushing inserts for
injection molding in high quantities
Thick-Walled Structures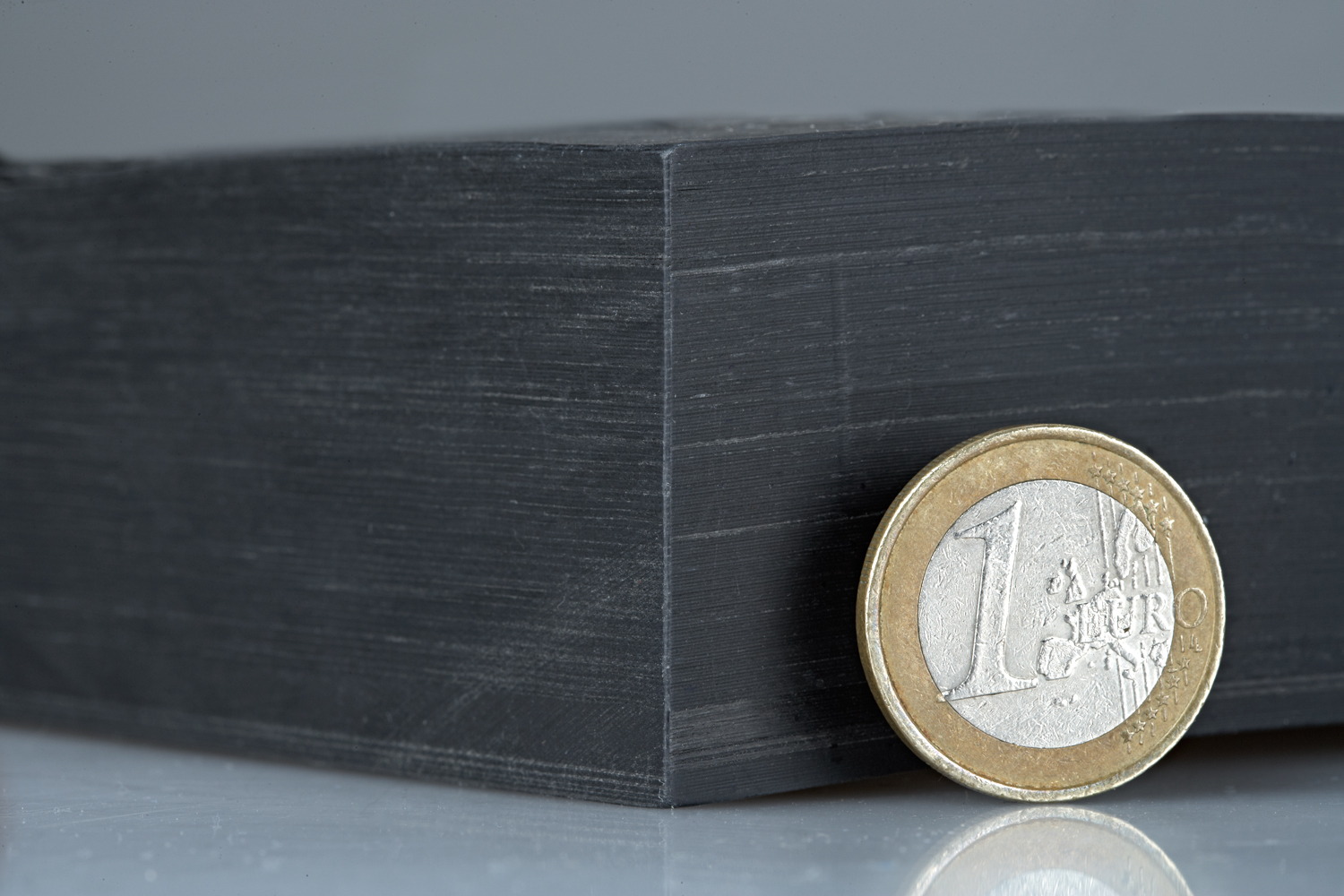
Thick-walled tubular structures from industrial seals to
booster rockets
Pressure Vessels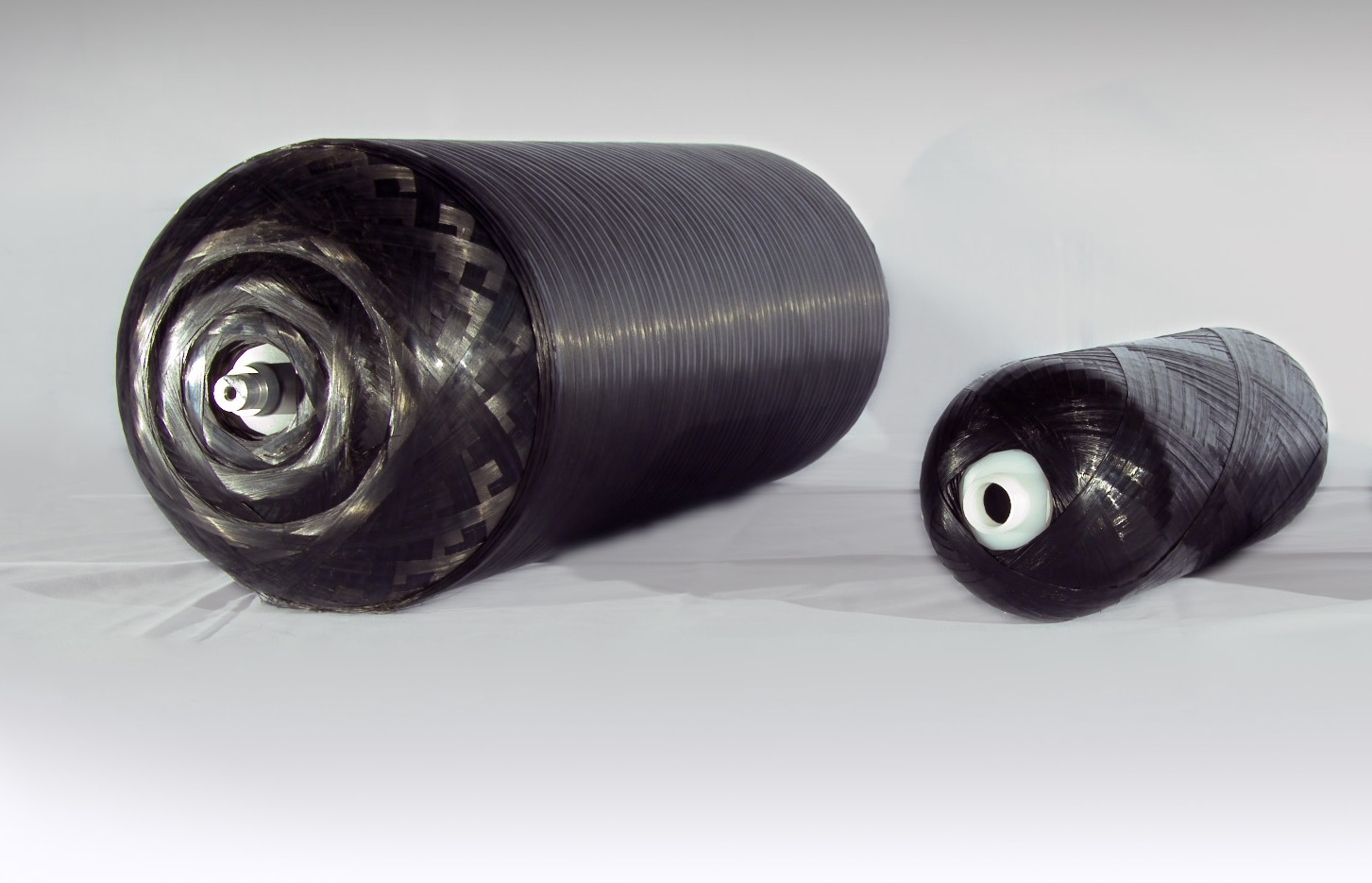
Vessels for high-pressure hydrogen or nitrogen even in cryogenic conditions
Functionalized Tubes
Functionalized tubes through bending,
reforming or over molding